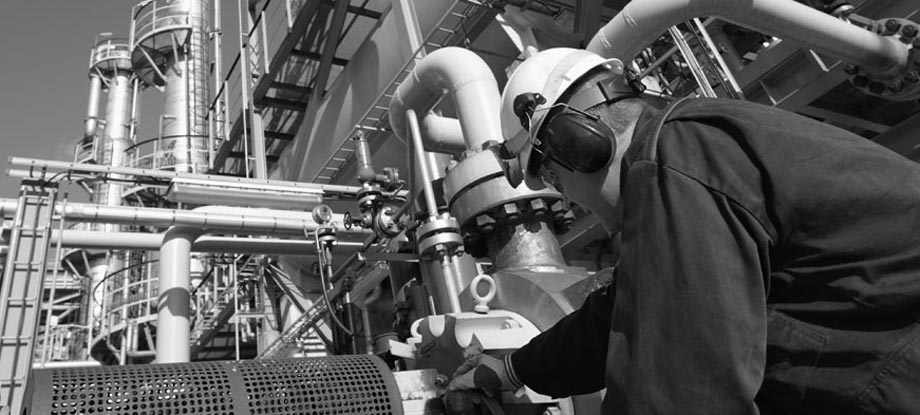
Cos’è la manutenzione Lean?
Nell’ultimo decennio, il fenomeno “Lean” ha permesso alle industrie manifatturiere di aumentare notevolmente i livelli di redditività e produttività. In combinazione con altre iniziative come Total Productive Maintenance (TPM), la Lean ha incoraggiato queste aziende a concentrarsi sull’efficienza dei loro processi produttivi.
Nell’ambito della manutenzione, la nostra esperienza ci ha insegnato che, mentre si applicano gli stessi principi di base, il modo in cui vengono applicati deve essere modificato da quello tipicamente applicato in un ambiente manifatturiero/assemblaggio, se si vogliono ottenere i massimi risultati. Un approccio di manutenzione snello non può essere solo l’immagine speculare di un approccio di produzione snello.
Perché implementare la manutenzione snella?
Molte organizzazioni sono cadute nella trappola di concentrarsi sugli strumenti e le tecniche associate alla Lean invece che comprendere la ragione del loro utilizzo.
In termini semplicistici Lean Maintenance è:
- fare la giusta manutenzione
- svolgere le attività nel modo più efficace ed efficiente
- un approccio potente per aiutare a identificare ed eliminare i problemi relativi agli sprechi e fornire reali miglioramenti (se implementati e gestiti nel modo giusto)
Approccio integrato per il miglioramento della manutenzione snella
L’approccio di miglioramento integrato della Lean Maintenance, che il VIT della WTCO consiglia e utilizza, applica i principi Lean in un framework adattato, nello specifico, alla manutenzione. Ciò garantisce che i principi vengano applicati nel modo più conveniente ed economico e in modo appropriato rispetto all’azienda di riferimento, portando così a miglioramenti rapidi e misurabili. Il quadro può essere ulteriormente adattato per soddisfare i requisiti specifici delle singole organizzazioni e i loro bisogni.
Dalla nostra esperienza nell’implementazione di iniziative di miglioramento continuo orientate in ambito Lean, TPM e non solo, sosteniamo un approccio alla manutenzione in 5 step:
- Restore of basic
- Autonomous Maintenance Calendar
- Breakdown Analysis and 5S Maintenance areas
- Professional Maintenance Calendar
- Maintenance Cost Optimization
Di seguito alcuni elementi su cui i 5 step andranno ad impattare:
- Moto inutile
- Viaggi non necessari, spostamento non necessario di beni mobili
- Viaggi in negozi di utensili o officine
- Ricerca di articoli
- Spostamento di postazioni di lavoro mobili senza una buona ragione
- Scarsa gestione dell’inventario – In un ambiente complesso, una scarsa organizzazione dell’inventario può produrre disordine e sprechi
- Rilavorazione – Ripetere attività o svolgere attività aggiuntive a causa di una scarsa lavorazione
- Sottoutilizzazione delle persone – Uso delle persone al limite delle loro qualifiche, non ai limiti delle loro capacità
- Gestione dei dati inefficace – Raccolta di dati inutili o impossibilità di raccogliere dati di vitale importanza
- Applicazione errata del macchinario
- Funzionamento errato o strategie operative deliberate che portano a costi elevati o a lavori di manutenzione quando non è necessario
- Utilizzare strumenti e tecniche che si allineano con l’eliminazione degli sprechi
Di seguito alcuni strumenti che devono essere inseriti e utilizzati per approcciare i 5 step:
- 5S – gestione e miglioramento del posto di lavoro
- Visual Management
- Mappatura del flusso di valori
- A prova di errore
- Creazione del lavoro standard
- Pianificazione
- RCM / PMO
L’implementazione di un ciclo di miglioramento basato su un intervallo temporale predefinito (in genere da 10 a 12 settimane) necessita di essere sostenuto con disciplina e con la partecipazione di tutti. Per questo sarà fondamentale istituire un programma di governance per garantire risultati misurabili e sostenibili nelle prestazioni organizzative.
Gestire gli sprechi a livello di organizzazione associati ai processi aziendali, ai sistemi, alle tecnologie e alle persone permette di incrementare la capacità di raggiungere obiettivi di produzione e di costo e porre le basi per futuri miglioramenti sostenibili.
Benefici della manutenzione snella
I vantaggi dell’utilizzo di questo tipo di approccio sono:
- Implementazione completa di progetti di miglioramento Lean mirati su un periodo di 12 mesi
- Rapido raggiungimento di miglioramenti delle prestazioni misurabili a breve termine
- Un programma Lean che può essere gestito e monitorato garantirà il miglioramento a lungo termine
- Coerenza di approccio per i futuri progetti di miglioramento Lean
- Personale completamente addestrato sui principi della manutenzione Lean
- Esposizione ampia del sito di manutenzione snella
In tutto questo, prestare grande importanza e attenzione alle risorse, le persone, ovvero muoversi verso il change management, diventa un elemento fondamentale e indispensabile al fine di creare una cultura del cambiamento e dell’approccio verso una manutenzione produttiva.
In merito ai risultati ottenuti attraverso l’approccio di manutenzione, consulta la nostra ultima case history
Per ulteriori informazioni su Lean Maintenance e su come WTCO attraverso il VIT potrebbe aiutarti a fornire miglioramenti reali e sostenibili, contattaci al numero +39 348 8988989 o via e-mail all’indirizzo commerciale@wtco.global